7 Common Mistakes Businesses Make With OSHA Compliance
7 Common Mistakes Businesses make with OSHA Compliance
Navigating OSHA compliance can be tricky for many businesses. Missteps can lead to serious consequences, including hefty fines, legal troubles, and even workplace accidents. Let's explore some common mistakes businesses make when trying to stay compliant with OSHA regulations and how to avoid them.
1. Neglecting Employee Training
Effective training is essential for fostering a safe work environment. However, many organizations neglect this aspect by failing to offer sufficient training or refreshers, which leaves employees ill-equipped to handle potential dangers. This lapse can escalate the likelihood of accidents and injuries, which may initially appear preventable. For instance, an employee who is unaware of the latest safety regulations might misinterpret warning signs or mishandle machinery, resulting in severe repercussions. Regularly updating training programs ensures that all personnel are aligned with safety protocols. Moreover, integrating interactive and hands-on elements into training sessions, as advised by OSHA, can significantly improve the absorption and retention of crucial safety information.
2. Overlooking Workplace Hazards
Failure to identify and mitigate potential risks can result in accidents. Conduct regular inspections to ensure all hazards are addressed promptly. It's essential to empower employees to speak up about possible dangers they encounter in their daily tasks. By involving workers in hazard identification, businesses can foster a culture of safety and awareness. Besides, the involvement of frontline employees often reveals overlooked risks that management might not be aware of. Leveraging employee buy-in can enhance hazard identification and prompt timely corrective measures. Regular meetings and open forums where employees can voice their safety concerns without fear of retribution are instrumental in this process.
Once these hazards are identified, they must be documented thoroughly and addressed with appropriate measures. Implementing robust risk assessment processes ensures that identified hazards are prioritized and remedied quickly. Using technology, such as safety management software, can streamline this documentation and tracking process, thereby reducing response times and enhancing preventative strategies.
3. Ignoring Documentation Requirements
Accurate and complete documentation is essential for demonstrating compliance. Businesses often face issues due to missing or incomplete records, leading to penalties during audits. For many, the documentation process might seem bureaucratic, but it is a cornerstone of OSHA compliance and effective safety management. OSHA requires that all incidents, no matter how minor, be documented in detail. This includes not only accidents but also near misses, as they can provide valuable insights into potential organizational vulnerabilities.
Moreover, fostering a habit of thorough documentation helps in trend analysis, which can reveal repeating patterns of incidents, assisting in proactive risk management. Ensuring that records are consistently updated and made readily accessible to auditors can significantly reduce compliance risk. Adopting digital solutions for maintaining OSHA compliance documentation, such as electronic safety data sheets, can enhance the accuracy and availability of required documents.
4. Underestimating the Importance of Personal Protective Equipment
Providing and enforcing the use of personal protective equipment (PPE) is vital. Businesses can find themselves in violation when they fail to supply necessary PPE or ensure it is properly used. The selection of PPE should be based on a comprehensive understanding of the specific hazards present in the workplace environment. For instance, in industries exposed to high temperatures, such as construction or metalworking, PPE for heat resistance is non-negotiable. Employees should be trained on the correct use and maintenance of PPE to ensure it remains effective and does not, inadvertently, create additional hazards.
The culture around PPE usage should be one of diligence and understanding, not simply compliance. Engaging employees in the selection process can improve acceptance and consistent usage. Reviewing and updating PPE policies regularly ensures that changes in technology or job roles are reflected promptly. Furthermore, integrating periodic checks on PPE conditions into regular safety audits can highlight any wear and tear, ensuring replacements are made as necessary.
5. Failing to Stay Updated on OSHA Standards
OSHA regulations are constantly evolving. Businesses often make mistakes by not staying informed about new standards and failing to implement changes effectively. This reactive approach can lead to compliance gaps and potential fines. Staying updated requires a proactive mindset, where businesses regularly review and assess current practices against revised OSHA criteria. Engaging with industry seminars, workshops, and subscribing to OSHA updates are excellent ways to stay informed.
Moreover, organizations must allocate resources for continuous training to ensure all employees are up-to-date with the latest standards. Creating an internal compliance team or consulting with external safety experts can aid in this continuous loop of education and implementation. By anticipating regulatory changes, businesses can position themselves as leaders in safety excellence, reducing incidents and enhancing employee well-being.
6. Inadequate Emergency Preparedness
The absence of a robust emergency plan can lead to dire consequences during a crisis. It’s essential for your business to have a clear, well-communicated strategy and to conduct regular drills to ensure everyone is prepared. Emergency preparedness goes beyond having a documented plan; it involves making certain that each employee understands their specific responsibilities in an emergency. Regular training sessions and simulated drills can significantly enhance staff readiness and response times.
Developing comprehensive emergency plans that address various scenarios, such as fires, natural disasters, and chemical spills, empowers employees to act decisively and calmly. Additionally, technology plays a vital role in emergency preparedness by offering tools like automated alert systems and centralized communication hubs. Investing in these technologies improves coordination and the flow of information during critical times. Fostering a culture of preparedness reinforces a business's dedication to safety and elevates overall morale.
7. Ignoring Feedback from Employees
Employees are often aware of potential issues before management. Ignoring their feedback can lead to unresolved hazards. Encourage open communication and act on employee insights to maintain a safe environment. With employee feedback, you gain firsthand knowledge of on-the-ground conditions, which can be instrumental in refining your safety strategies. Creating a structured approach for collecting and acting on this feedback boosts employee engagement and fosters a cooperative safety culture.
Implement systems for anonymous reporting to ensure employees feel safe in sharing genuine concerns without the fear of retribution. Prioritize these reports, investigate promptly, and communicate actions taken to address them. Additionally, conducting regular surveys or hosting town hall meetings centered around safety can also encourage dialogue and exchange between management and staff. Not only does this approach improve safety, but it also enhances trust and transparency within the organization.
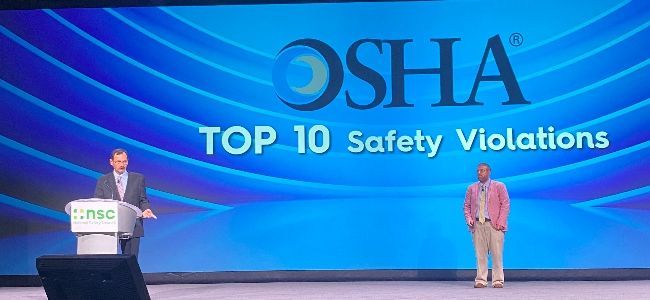