The Comprehensive Guide to Forklift Training: Best Practices and Benefits
Introduction to Forklift Training / Best Practices
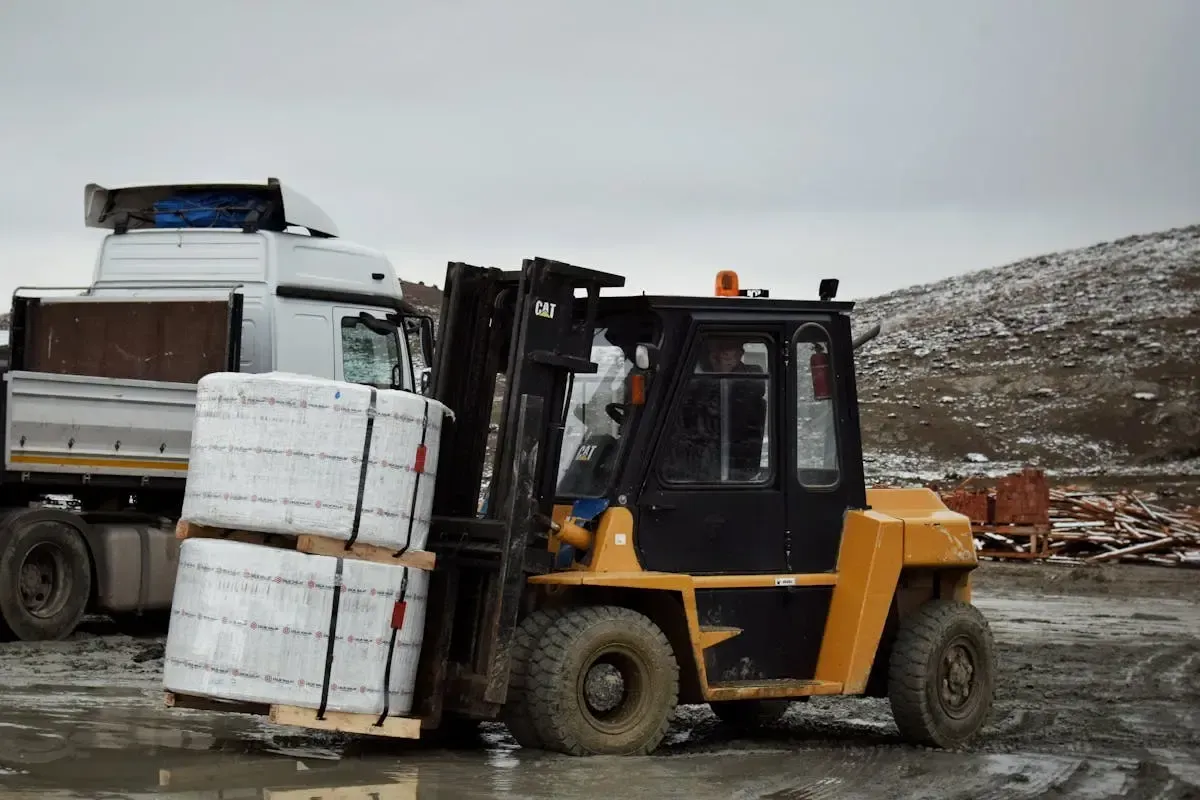
Introduction to Forklift Training: Why It Matters
Forklift training isn't just a good idea—it's essential. Operating a forklift might look easy, but it's more complex than you think. Without proper training, the risk of accidents and damage shoots up. Forklift training gives drivers the know-how on safe operation, making workplaces safer for everyone. It teaches vital skills like steering, loading, and maintenance, ensuring operations run smoothly. Plus, it's not only about safety. Trained forklift operators are more efficient, reducing product damage and saving money. Every year, accidents related to forklifts cost businesses loads of cash and, worse, can lead to serious injuries or fatalities. By investing in training, companies show they value safety and their employees, leading to a healthier work culture. In short, forklift training matters a lot—it's the key to safe, efficient, and productive operations.
The Key Components of Forklift Training Programs
Forklift training programs have some core elements that ensure operators are ready and safe. First off, these programs cover how to handle forklifts safely. This isn't just about driving; it's also about knowing how to load and unload without causing damage or injuries. Then, there's understanding the forklift itself - its parts, how it works, and its limits. Good training also dives into workplace specific safety practices. Every work environment is different, so knowing how to navigate yours with a forklift is critical. Most importantly, these programs emphasize the importance of regular inspections and maintenance of forklifts. A well-maintained forklift reduces the risk of accidents. Lastly, effective training isn't a one-time thing; it includes regular refresher courses to keep skills sharp and knowledge up to date. Remember, the goal is always to keep everyone safe and operations smooth.
Understanding Different Types of Forklifts and Their Uses
Forklifts are not all the same, and knowing the differences is key before jumping into training. Firstly, let's talk counterbalance forklifts. These are the most common. They have forks at the front and a weight at the back that keeps them balanced. They're your go-to for moving pallets and boxes. Then, there are reach trucks. Ideal for warehouses with high shelves, these can stretch out their forks to pick stuff up high without moving the base. Very handy! How about pallet jacks? These are simpler and are great for moving stuff short distances – think of moving deliveries in a grocery store.
Next up, we've got side loaders. These come into play when dealing with long and heavy stuff like timber or pipes. They carry the load at the side, making it easier to navigate narrow spaces. Lastly, telescopic handlers, or telehandlers, are like the Swiss army knife of forklifts. They have an extendable arm, making them perfect for tasks requiring reach and versatility, such as in construction and agriculture.
Each type has its own perks and is designed for specific tasks. So, knowing which forklift to use is crucial for safety and efficiency on the job.
Best Practices for Safe Forklift Operation
To safely operate a forklift, it's crucial to stick to best practices that ensure everyone's safety and keep the work flowing smoothly. First off, always check the forklift before you start it. This isn’t just a once-over glance; look at the brakes, steering, controls, and warning devices. If something seems off, report it. Don’t just push through and hope for the best. Now, when driving, keep your load low and tilt the forks back to stabilize the load. Seems simple, right? But it’s easy to forget in a hurry. Also, always stay within the forklift's operational limits. This means not going too fast and not lifting more than the forklift can handle. Overloading is a fast track to accidents. Speaking of speed, always drive at a speed that lets you stop safely. Conditions can change, and what was a clear path a minute ago could now be a hazard. Awareness is key. Be aware of your surroundings, other workers, and any obstacles or changes in floor conditions. Lastly, communication is crucial. Use signals, make eye contact with other workers, and if needed, use a spotter to guide you. These practices might seem straightforward, but they are the backbone of safe forklift operation. Stick to them, and you reduce the risk of accidents significantly.
The Benefits of Effective Forklift Training
Effective forklift training is more than just meeting regulations; it offers a host of benefits. Firstly, it significantly reduces the risk of workplace accidents. Forklifts can be dangerous if they are not operated correctly, and proper training ensures that operators know how to use them safely, protecting both themselves and their colleagues.
Secondly, there's the efficiency angle. A well-trained forklift operator is like a well-oiled machine—productive and reliable. They can move goods faster and with fewer mistakes, which is good for business. It means projects stay on schedule, inventory is managed correctly, and the company saves money.
Thirdly, let's not forget about the equipment itself. Forklifts are expensive, and mishandling them can lead to costly repairs. Training teaches operators how to use forklifts the right way, which extends the life of these machines and saves the company from unnecessary expenses.
Lastly, effective training boosts morale. Workers feel more confident when they know what they're doing, and this confidence translates into better job satisfaction and loyalty, which in turn reduces turnover. This is a win-win for everyone.
In short, effective forklift training keeps people safe, makes the operation more efficient, saves money, and keeps workers happy. It's more than just a checkbox on a compliance form.
The Role of Certification in Forklift Training
Getting certified to operate a forklift is more than just obtaining a piece of paper; it's a crucial step in ensuring safety and efficiency at work. When it comes to forklift training, certification is not just an added advantage, it's mandatory. According to Occupational Safety and Health Administration (OSHA 1910.178), to legally operate a forklift at a workplace, you need to be certified. The certification process involves classroom learning, hands-on training, and successfully passing a test. By getting certified, you not only prove that you know how to operate a forklift, but you also demonstrate your knowledge of safety practices, which can significantly reduce accidents at work. Furthermore, obtaining certification can open doors to better job opportunities and potentially higher pay. In short, forklift certification is the key to becoming a proficient and safety-conscious operator. If you're interested in forklift/lull operator training, reach out to Trident Safety Company and inquire about the Train The Trainer (TTT) Forklift training.
Common Mistakes to Avoid During Forklift Training
When training on forklift operation, several common slips trip people up, slowing down their progress. First off, skipping the basics is a no-go. Every operator needs a solid grounding in the fundamentals of forklift use—thinking you can leapfrog this stage is a mistake. Then there's the issue of not respecting the forklift's weight and power. These machines are heavy and can be dangerous if not handled with the proper care. Underestimating this leads to accidents. Also, ignoring the importance of regular checks and maintenance is a shortcut to breakdowns and potential safety hazards. Forklifts need to be in top condition to operate safely. Another misstep is neglecting the specific training for different types of forklifts. Not all forklifts are the same, and knowing how to operate one type doesn’t mean you can handle them all. Lastly, overlooking the need for refresher courses is a blunder. Skills get rusty without practice, and regulations change. Continuous learning is key to staying sharp and safe. Avoid these pitfalls to ensure your forklift training sets you up for success, not failure.
Post-Training Evaluation: Ensuring Skills Retention
After forklift training wraps up, it's crucial to not just pat backs and hand out certificates. Evaluating if a trainee truly got the hang of operating a forklift is where the rubber meets the road. This step checks if the training sticks or if it slipped through like water. How? By setting up real-world scenarios or simulations that mirror daily tasks. This way, evaluators can see in action if the trainees can safely and efficiently maneuver the forklift. It's not just about did they pass or fail. It's digging into areas that need a polish or where they shine. Feedback is direct and to the point, focusing on highlighting strengths and pinpointing weaknesses without beating around the bush. This ensures trainees not only know how to drive a forklift but drive it right in the situations they'll face daily.
Conclusion: Maximizing the Impact of Forklift Training
In wrapping up, the true worth of forklift training goes beyond just meeting legal requirements. It's a solid investment in safety, efficiency, and long-term savings. By embracing best practices in forklift training, businesses not only protect their employees but also boost productivity and reduce costly accidents. Remember, it's not just about ticking off a box for compliance; it’s about fostering a culture of safety and excellence. Continuous training updates and refreshers are key, ensuring skills remain sharp and updated with the latest safety protocols. Being diligent in training pays off, literally reducing damage to goods and equipment. To sum up, effective forklift training is invaluable. It saves lives, protects assets, and enhances operational efficiency. Don't just do it because you have to—do it because it makes a significant difference.
If you're interested in forklift/lull operator training, reach out to Trident Safety Company and inquire about the Train The Trainer (TTT) Forklift training. www.tridentsafetyco.com
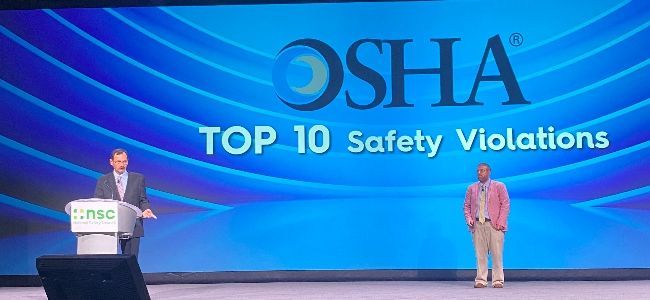